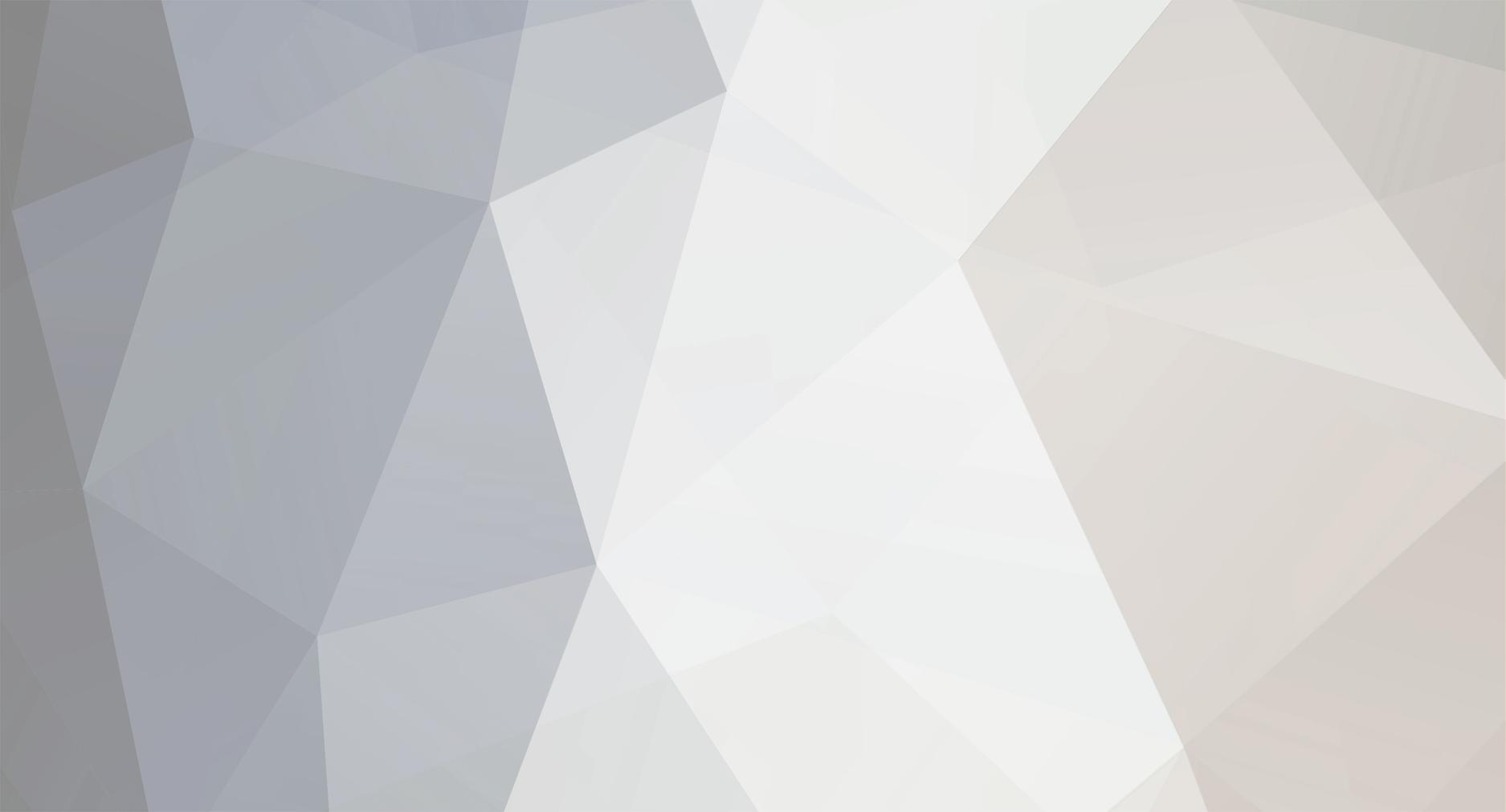
BKB94
Members-
Posts
256 -
Joined
-
Last visited
-
Days Won
20
BKB94 last won the day on November 25 2024
BKB94 had the most liked content!
Profile Information
-
Location
PA
Previous Fields
-
Zip Code
18092
-
Model Year
1987
Recent Profile Visitors
The recent visitors block is disabled and is not being shown to other users.
BKB94's Achievements
-
Blown Head Gasket Engine Rebuild...What did ChatGPT Say?
BKB94 replied to nc_beagle's topic in Just plain ol' B.S.
Its always good to get a health check on a engine before disassembly. I at the minimum would want actual oil pressure readings hot at idle and where the bypass is, compression test and leak down test. You will have 1 or 2 cylinders that will give you poor reading do to the HG blown probably but it will let you know the conditions of the rings, cylinders, valves, jet valves, head if cracked. A few minutes can give you a lot of info. -
Man I keep getting distracted. Poor Mustang hasn't been touched in 20 years and I had that feeling that I need to really go over it. On the lift I drained the oil and noticed long thin slivers of metal on the magnet and was glad I was pulling the engine for a health check. Have some new Maximum Motorsports suspension parts that have been is storage for years that's finally going on the car. Blew the car apart and painted and powdercoated everything underneath. Built a 1999 8.8 rear with 31 spline axles, T2 diff, 3.73 gears along with 14" rotors and the torque arm. The engine ate the cam gear for some unknown reason and the T-chain was very worn for the low mileage. Working with the vendor now as to why these custom pieces failed so early. I will be adding a new supercharger case that breathes a lot better this should add about 30 hp and tq. That should put me around 430 rwhp and almost 500tq, that makes for a very fun car.
-
No headlights, TS, Brake lights…fog lights
BKB94 replied to Mike7447's topic in Newbie Question and Answers
Keep hooking up temporary grounds, Your on the right track. -
Should be nothing in the passenger side wiring harness, I removed it its all EEC.
-
conquestcobra started following BKB94
-
I pulled the HVAC and replaced all the foam on flapper doors and I'm very glad I did. Everything I touched turned to dust so no way any of it would have sealed, plus condenser was very dirty.
-
And just like the early 2000s no pictures. Useless thread.
-
Mini update. 2 big mistakes were fixed recently. First car had a engine vibration right off idle that I could not figure out and a constant cylinder 6 contribution error. Decided to pull the trans to verify it had a 50oz flywheel, this was not as bad as I was anticipating. I installed the engine and trans together from underneath so at first I didn't even know if it was possible to pull just the trans. The new flywheel on the bottom is a 50oz and looks like every other 50oz flywheel I have ever seen, what was in the car I have no idea. It was not a 28oz flywheel ironically its marked 41 and with the drilling I could see that. No ford that I know of uses such a imbalance. So new flywheel is in and its smoother but still does not seem 100% but then I remembered the transmission mount is solid chunk of rubber not like the supper soft OEM ones I'm used to. My 2nd issue was oil consumption and a vacuum leak that was causing high idle. Well this was me not knowing the aftermarket heads drill the rocker bolt hole straight thru the intake runner. Had to use sealant on the rocker studs to fix the oil and vacuum issue. Still beating on this thing around the village with no doors or hatch, its so much fun and feels like it has 400hp but it doesn't. Then I got distracted and made a very bad decision.
-
You can make different strut catriges fit our housing but the strut is very tall and when lowered you run out of travel. You can cut the housing down and use a cut a strut with a universal gland nut. Or just buy D2s
-
Been busy but not on the quest. My uncle passed and his house is 3hrs away so every weekend has been cleaning out the house. The truck hates me and cracked a head and lost a caliper. Barn AC had a leak and I can't work in this heat, so brazed in some patches on the condenser and its back in action. Started getting my dads barn cleaned up and the wiring failed in the ceiling and no light and most receptacle's dead. Waiting for the heat to calm down to clean, add more lighting, and build the paint booth. Back to the build. A/C So I have been wanting to get the A/C charged and check one thing off my list. Pulled a vacuum and weighed in a charge, was using a Fox mustang as an idea how much it would take 28-32 OZ. I knew the AC worked before because I heard the clutch pulled in months ago when I had a nitrogen charge in it to leak check. But no matter what I couldn't get 12V from the HVAC control. Then you start doubting all your work so I had to beep everything out to confirm its correct. Once all was confirmed I replaced the HVAC box and again I heard the clutch kick in then release soon later. Check the voltage and I would get 3.5 VDC off wire 36 so I'm damaging the output of the HVAC control. My mistake was that when you here AC clutch relay you would assume the relay is putting the load across the contacts with a 15amp fused supply. But I come to find that ford inside the CCRM is using a NC relay for WOT cut out. So I need to add a 15 amp fused power to a A/C relay probably behind the dash, many fused circuits are not being used do to the CCRM. Pin 21 is 12V from HVAC through my aftermarket trinary switch and then into the CCRM. Here is the Trinary switch, drier, CCRM. Still extremely happy with the clean set up, not that it was hard to make it nicer then the rats next that Mitsubishi made. But the best part is it works awesome, 92'F and humid with no doors or hatch and 36'F out the vents. Ended up dumping 2 pounds in it and my pressures are still low by 15psi but good enough for now. This junkyard 5.0 So after re-torquing the lower intake I had lots of weird issues and its getting worse. Its in a high idle and burns oil, worse the warmer it gets. So I'm pretty sure the lower intake needs thicker gaskets and the ports are open at the bottom of the ports sucking in oily vapor. Will probably address this before paint.
-
Driveshaft gone still have crossmembers
-
2618-4032- Hypereutec, Cast. A piston discussion
BKB94 replied to Mike7447's topic in Virtual Mechanic
I love hyper pistons with a competent machine shop that hones it properly with a deck plate. You can have any piston made any way you want it, cost used to be negligible over off the shelf pistons. As always forged pistons give you head room for poor tuning, high EGTs, detonation. But honestly with all the OEMs using hyper pistons with direct injected turbo engines I have never seen an engine failure do to the piston failing, even with massive HP tunes. I would pick a light hyper piston that uses a modern ring package but not low tension. You could go gapless rings but I still have oil consumption issues with the gapless second ring. My leak down is almost un measurable but I have yet to get the PVC dialed in to where under deceleration I’m not pulling oil into the manifold. Might be a roots blower specific issue. -
My experience with the ready to spray cans is its very thin and does not cover well. I did a dark green fender and it took 3 cans, your result may very.
-
Redhead unfortunately is not what it was 10 years ago. Lots of poor customer service reports for bad steering boxes. Might be your only option though. Check with blue top and see if they will touch it. Although blue top is having staffing issues themselves since no one seems to want to work anymore.
-
Front strut KYB cartridge loose after tightening?
BKB94 replied to Mech's topic in Just plain ol' B.S.
Think spec is .040 thread exposed on gland nut when tight. Best method is to find pipe that fits the nub on the bottom of the strut and make a spacer like they were when new. Maybe post pictures, don’t understand why no one ever post pictures. the struts on the left are missing the spacers that came with the Bilstein strut inserts, ones on the right have them on. Do you have those on? Either way that's what you need and how you would want to fix this issue. Machine shop might do this for you but not worth their time. Unless KYB are totally different, every cut a strut I have done has a nub on the bottom for spacers.