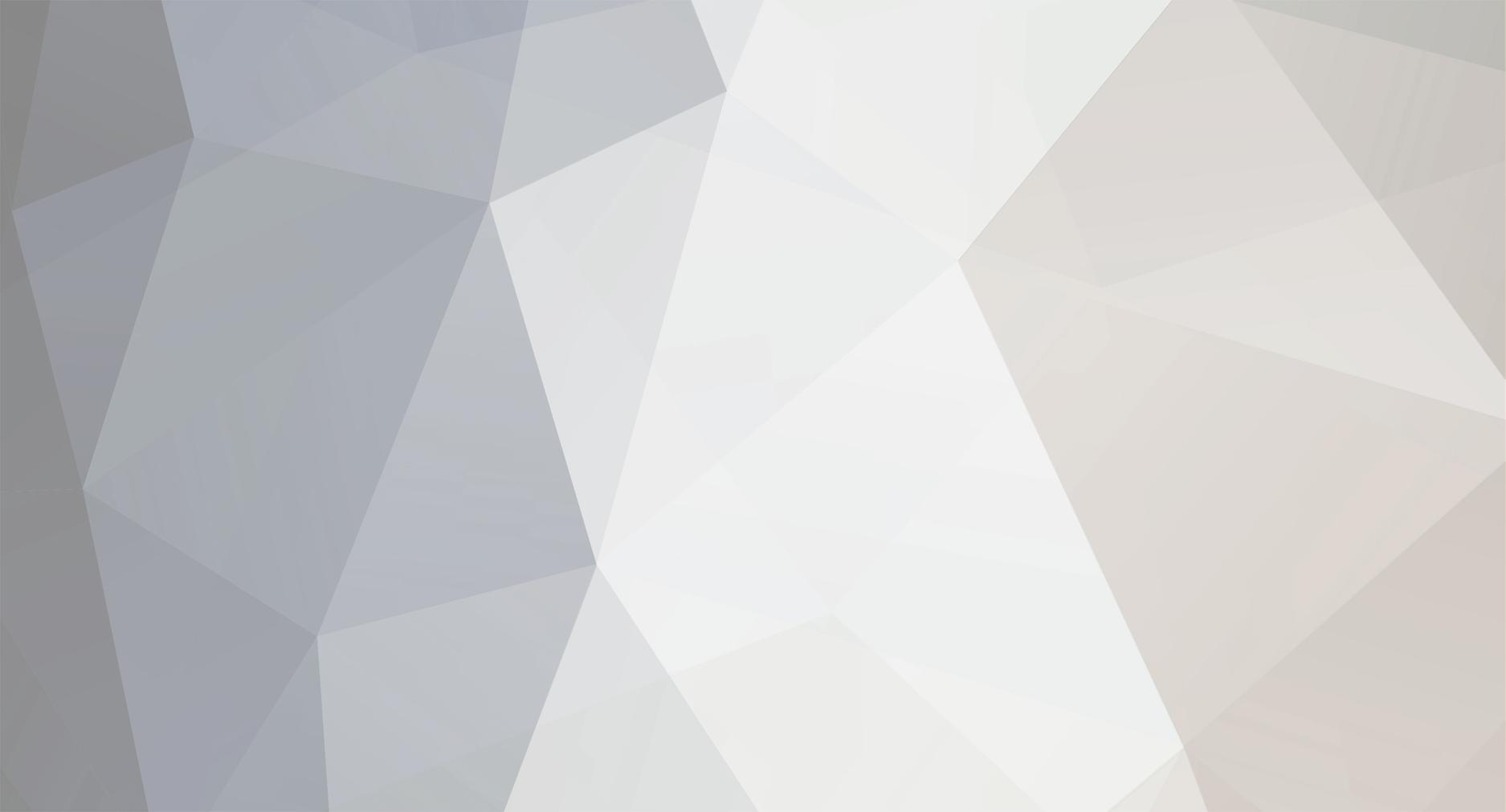
Wolf87Conquest
Members-
Posts
471 -
Joined
-
Last visited
Content Type
Profiles
Forums
Calendar
Gallery
Everything posted by Wolf87Conquest
-
With the tach jumping while cranking, injectors should fire. I'd suggest testing with a meter that one side of the injectors has 12v. It should always be there. Then check ground at the ECU and the ground to injectors from ECU. The ECU fires the injectors with the ground. Air or a clog in fuel system will have an effect as well.
-
Could it be anything but...........
Wolf87Conquest replied to TopDawg_43's topic in Virtual Mechanic
Vavle guide, even valve seat can drop and make a valve hang. Pulling the head and careful inspection of all the parts will have the answer as to what happened. You said the car sat for several years, could be the spring is "locked" or bound. Anything in the vavletrain or head could be suspect. Just need to pull the head and see. -
Electrical Issue (power only to interior lights)
Wolf87Conquest replied to freetoskate124's topic in Virtual Mechanic
Check to make sure the new links are connected solid. Use a meter to check. Then check fuses, again make sure of good, solid connections. Won't hurt to meter the circuit to the ignition switch. Including grounds. Should find the problem easily. -
It's a good idea to get the wire harness from the doner car. If nothing else, it will make sure you have it wired correctly.
-
87 Conquest TSI, white, in western Pa
Wolf87Conquest replied to Wolf87Conquest's topic in Cars for sale
I am 50 miles north of Pittsburgh in a town called New Castle. Seats are burgundy leather. Pics are one the following webpage. I'm on webtv and do not have digital cam or any way to post recent pics, the ones on the page are from shortly after purchase in 03. http://community.webtv.net/MrMopar-wolf/MyCartitle/ E-mail me MrMopar-wolf@webtv.net with Conquest in subject line if you are interested in seeing the car for address info or any other questions. -
Must sell my non running TSI. Needs a little body work, one front tire, battery and might need a little electrical clean up/repairs. Was running good before I had to park it when license was taken. 87 widebody, 5 speed manual, mostly stock, custom graphics, 89 specs in ECU, new tires (but does need one new front tire as it was slashed), new rear brakes and calipers before being parked, new flex brake lines up front, new windshield, new diff mounts. Looking for any reasonable offer over $400 and will be sold as is. Car is in western Pa. Will need to be towed by buyer at time of sale. Any questions or you would like any further details feel free to e-mail me MrMopar-wolf@webtv.net with Conquest in the subject line. This car must be sold and with a little TLC can be on the road again. The car is in fair condition, body needs a little work, mechanically very sound as far as I know, interior needs work (torn seats). The car is white with burgundy interior.
-
I don't know the answer, but I believe 86 and earlier used the same injectors for both and fired them alternately. I would think it safe to assume the wiring and electrics you are concerned with would be similar enough to follow the 86 system. I could be wrong, but it seems logical.
-
Replacing a clutch is fairly straight forward. Check all related parts, like clutch master cylinder, slave, U joints, and pivot points for wear etc. Might be a good idea to replace the fluid. The flywheel should be resurfaced, same manner as brake rotor, and for the same reason.
-
To be that cruddy and still work at all...you got a good strong motor. A good clean up, replace lube, check it electrically (good continuity) should be all it needs. Make sure you keep polarity correct. The motor's communtator may need a good cleaning, good motor brushes and brush springs, motor bearing lube it will be good to go for many years. General clean up and lube on the wiper arms would be a good idea as well. An electric motor repair shop should have brushes, brush springs and bearings if any are needed.
-
It's a whole lot easier to replace the mounts than to remove and wrestle in the diff cradle (what you are calling the subframe) unless you have help. Jack the rear enough for acess and support safely. Two nuts each side inside a "notch"...swivel needed to get the right angle on them. I'd give them a shot of PB Blaster and let sit a while, then try them. Then there is one nut on top each side. You'll need a jack to hold the diff...and help move it when needed. I had to replace the mounts on mine, but the nuts in the "notch" were already a bit chewed and very rusty. Ended up using a Dremel tool and a cut off wheel to cut the bolt heads under the rubber of the mounts. It's an option if needed. The ones on top that mount the diff itself are easy to get to.
-
Sounds like you had a loose connection when you were "throwing" parts at it. With electrical problems...the best thing to do is start testing the problem circuit with a meter. My prefered method is disconnect the car's battery and with meter set on Ohms, check continuity. The problem almost always shows up within 5 minutes. This method pinpoints exactly where the problem is...bad/dirty connection, failed part, or broken wire. Then you replace only failed parts, save hassle, money and time. Electrical problems can be a pain, but with the above method of testing, it can be found and corrected easily in most cases. Stress and panic free. If you don't have a multimeter...get one. Should be in any auto repair toolbox. You'll be glad you did. Also get extra long meter leads...comes in handy when you need to go from the battery cable to things like fuse box under dash. A good idea to have on hand a small soldering iron, solder, and shrink wrap in the most common sizes. Just in case you need it later.
-
Mild or completely stock engine....stock replacement should be good. Mild to heavy mods (or planning future upgrades) then any high energy coil would be best. Lots of companies make them, question is...what's available as a replacement and how much you want to spend. Some high energy coils these days offer multi spark capability...to use that function you'd need to switch the ignition module with a multi spark unit. Mallory makes coils and modules, been around a long time as well. There's no need to go high energy coil (or ignition system) unless you already have or are planning major modifications to the engine and systems. Stock to mild mods should not need that hot a spark...so I'd stick with the stock unit in this case.
-
tools needed for transmission removal/install
Wolf87Conquest replied to TheWormForEver's topic in Virtual Mechanic
Basic hand tools will work...fancy ratchet wrenches make it a bit easier...but I like a bending/swivel ratchet handle with normal sockets. Just seems the handle is tougher and can take more torque before breakage. Clutch tools like centering the bearing type tools..seal sets/puller etc. Plenty of shop rags...collector bins (fluids and parts). A floor jack will work, but I would add a strap to hold the trans securely to the jack for safety. Ziplock bags for the bolts/small parts...mark the bags as to where the bolts/small parts go to...easy install without hassles this way. Portable shop light is a very good idea. A can of PB Blaster for the rusty/cruddy bolts. A helper is always welcome...handing out tools, steadying large/heavy parts..heck even making jokes helps make the job easier and can make a beer run!...lol -
If the car was vibration free before the new tires....it would stand to reason the tires and balancing is not where it should be. If you swapped wheels and used the same tires...I would think you got a "bad" tire(s). It's known to happen that tires can be made wrong....shell, bead, belts, even tread can slip thru their quality control. What I think might be happening the balancing done was ok...the belts within are not right somehow, and when the speed get high enough, the belts move and unbalance the wheel. This is assuming the car was fine before the swap. Many parts in the steering, suspension and drive train can cause this issue...all steering components, steering knuckle, wheel bearings, suspension parts/bushings in front...CV joints and suspension parts/bushings in the rear...all drive line parts from trans rearward as well as trans and engine mounts. I've even found an "out of spec" brake rotor can cause this.
-
This is one where more info would help narrow down where the problem may be. Transitional periods (idle to half throttle) can be tricky to figure out where to look. Is the engine at operating temps or cold? Does it gradually get better, or stay that way? Timing correct? I'd look at the normal sensors (Like O2, temp), vac hoses, vac advance, MAF to be certain all sensors are functioning properly and no vac leaks, and advance isn't sticking. From the post...I'd think fuel system is working fine, so I'd look to vac leaks etc. as possible problem area.
-
Headlights go up and down rhythmically
Wolf87Conquest replied to helrazr70's topic in Virtual Mechanic
If this happens when the nose area gets wet...I'd look carefully and test with meter the wiring and connections. Power still going to the motors when it shouldn't might be a problem in those areas. It's possible you might see a wire missing a little insulation..add water...you get the picture. Shrink wrap on any problem wires is the best cure. -
I've had the best success finding the parts I need from 2 sources...Rockauto.com and Rockville Mitsubishi which can be contacted online. Fan motors that can be taken apart (not the sealed units) there is another option...look for an electric motor repair shop in your area. Rebuilding what you have is hassle free when it comes time to install the motor...no rewire, no adapters etc. and is most often cheaper than replacement. The place I go to here in my small town even offers a guarantee on their work...and stand behind it. Fastest time from drop off to pick up was 2 days, the longest was 4 days...the replacement parts needed came late to the shop. I'm not sure new OEM motors are available, it's most likely a reman (rebuilt) one anyway. So why worry...I'd take mine in to be rebuilt. I get my same motor I dropped off back...no hassles, no worries it fits and has a guarantee. It's up to you...good luck.
-
Sounds to me one or more of 4 likely culprits...diff mounts, torque tube, U joints, CV joints. TT and U joints are better tested/checked once removed from the car. Diff mounts are easy to test if they have failed...safely raise the rear of the car enough for you to crawl under...then grab the diff and try moving it...it is a bit heavy so it will take some effort. You could try a short pry bar to carefully move it with....sometimes just looking at it you can tell...if it's not sitting completely square, mounts are shot. Look carefully at the metal plate(s) part of the mounts and the rubber block in between the plates...you'll see what I mean. CV joints...carefully inspect the boots...any cracks/tears/holes it's a good bet dirt and moisture got into the joint and destroyed it, or is in the process of destroying it.
-
When I start testing a circuit, I prefer to disconnect the battery and set meter on Ohms to check coninuity..will tell you much more than voltage test. The main reason is with checking coninuity, you are testing one wire/connection/area(part) in the circuit. It will pinpoint exactly where the problem is. Voltage test will show only where power is not flowing, not always where the problem area is. Why? Because if the ground is the fault, no voltage will flow...voltage test will give you the general area in some cases...coninuity the exact spot of the circuit. Coninuity test can also show where the circuit may need some cleaning or further scrutiny...regular wires/fuses/connections should show very little or no resistance.
-
I'm fairly sure the "name brand" cam companies, like Crane for instane, stamp or in some way mark their cams. Some companies regrind cam blanks from others, so it's sometimes hard to tell for sure who actually made it. You might want to carefully measure your cam and see if that company sells cams with that profile...it will take some time and research on your part to be certain if it is not marked by a particular company.
-
Best way is to use a multimeter and test the entire circuit....wires, connections, sensor and fan motor should give usefull readings...relays will not. A relay with a meter will only show if the activating coil is good, unless power is applied to the coil to change the relay's normal set. Test that part of the circuit too.(Relay coil power). Make sure the ground is good also. Relays are pretty durable...I'd guess a loose/dirty/broken connection or a faulty part...such as the sensor. Using the meter, you should easily find the problem...and repair as needed without the hassle of throwing parts at it and wonder why it won't work. Wire repairs should be done with shrink wrap and solder.
-
Cleaning the battery cables and posts should help. Did you check the fuse link running beside the engine? I believe this link is to the alternator. Cleaning the starter connections might help as well....dirty connections adds resistance, sometimes more than the battey can overcome. All connections on the start solenoid should be cleaned too. A piece of very fine wet/dry sandpaper can cean them up nicely..as well as a little shot of electronic contact cleaner. Can get it at Radio Shack.
-
If you have the correct injectors and it all is wired correctly...it should work fine. Both injectors should have 12 volts or nearly that to one side (or wire) with the key on. The ECU (engine computer) provides the ground to fire the injector. You'll need to check with a meter to verify that power is getting to the injectors. A noid light will help in seeing injector pulses to tell if the ECU is fine.
-
I'm not sure which it is, but from normal electrical situations, it's the positive. Positive is always the switched side. Being the pick up in the distrib is what switches the coil on and off to fire it...stands to reason that's where the tach signal is originating. If the car runs the signal is being generated and sent to the ECU...no tach signal it won't start. You may need to get a meter on the circuit to find the problem. Check grounds as well.
-
Did you test the bulbs, connections, wires with a meter? I find the best way to test any circuit is this method...disconnect the battery positive post and make sure it cannot touch the post. Set meter on Ohm's and put one meter lead on the begining part of the circuit to be tested and the other lead on the connection/wire/part next in line with where the first meter lead is...if the meter shows near 0 Ohms (infinity)...it's ok, if not, then that part of the circuit is suspect and needs repair. Go thru the ENTIRE circuit that needs tested...you should find the problem(s) easily. Do not forget that bulbs etc. also need a good ground to function and the ground part of the circuit should be tested as well. Automotive wires that need replacement or repair should never just be twisted together and wrapped in electrical tape....it's fine for TEMPORARY repairs only. Shrink wrap, solder and a good quality splice joint is the best way. Crimp connectors would be a decent alternative if you are not willing to do the above way. Correct size connectors and a good crimp tool should help.