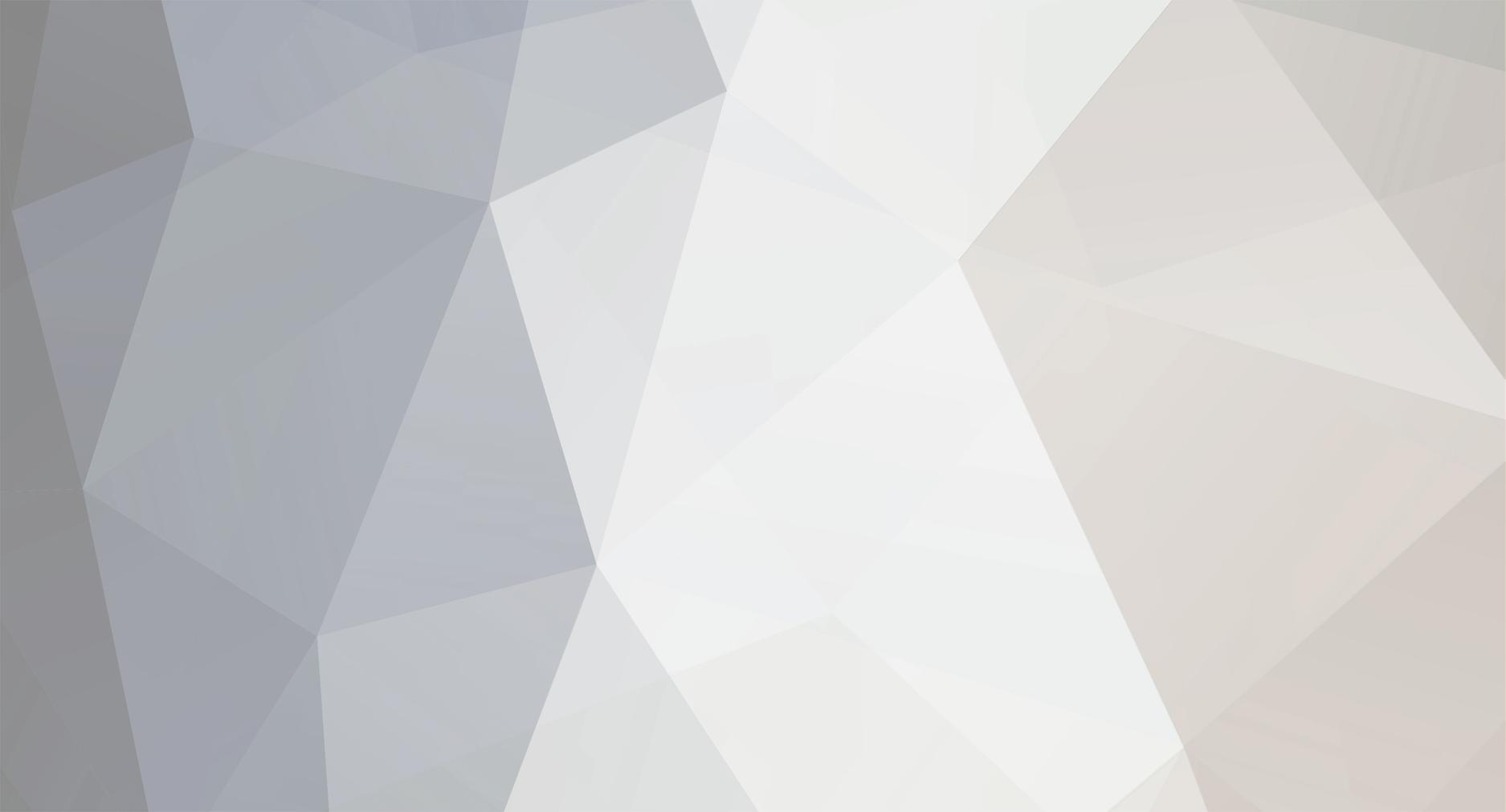
TurboRaider
Members-
Posts
153 -
Joined
-
Last visited
-
Days Won
1
Content Type
Profiles
Forums
Calendar
Gallery
Everything posted by TurboRaider
-
chrysler electronic ignition module....
TurboRaider replied to MontyTSI's topic in Engine and Performance Mods
A spark box thats good for 6000 RPM's on a 8 cyl will give you 12,000 rpms's on a four cyl since its putting out half as many sparks. As far as an easy module..... Our dist has an optinal self contained spark module. Just look at a dist from a Caravan, same basic design but with the spark control built in. Seems like a really easy way to get rid of the factory spark box. The unit is also very reliable and the instalation would be nice and clean. Personaly I like the factory box for my street 2.6. I do have it hooked up to a MSD 6. The detonation control works quite well with my 8.2 cr in a truck. Kevin C -
150-170 MPH Top Speed + Fuel Efficiency 5th Gear
TurboRaider replied to Oscar_the_Grouch's topic in Group Purchase Info
Look in the yard for early truck five speeds and you may find a fifth that when fitted (if it can be made to fit) to a starion box will provide a taller ratio.... I have seen the part but I have no idea what it came out of. It had the same final ratio because the reduction to the counter shaft was steeper..... The best i can promise is that there is a factory gear cut on the same sahft to sahft center line as your five speed with a taller ratio... The rest of it needs to be figured out. Kevin C -
Last I checked Redline was PAO based... As far as its life expectancy... I have been using Redline for years and never had a problem. Same with Mobil's gear lube. I did use AmsOil's gear lube way back in the 80's .. Put it in three trany's and all three developed noisey bearings within 5000 miles. Kein C
-
BSE mod. Free if you have the stuff
TurboRaider replied to Adi's topic in Engine and Performance Mods
Personal experiance.... 9:0 to 1 is a bit high. I was at 8.7 for a while and if I kept the boost to aobut 9-10 psi I was fine. 8:0 to 1 IMHO is a much better and a good maximum for higher boost. Kevin C -
Double coil ignition systems
TurboRaider replied to star_power's topic in Engine and Performance Mods
I would like to understand why this should help..... Â Its in my nature to question how things work. Â I cannot agree with a blanket statement that this will not hurt the ECU. Â Yours may be fine, but there may be other examples where doubeling the current will cause damage. A single coil draws 5 ams or so.... Two get you to 10 amps! That a lot of current. You cannot gaurentee based on a sample of two that this will not cause damage the drive transistor in every vehicle made. Also failure may not be instant..... over stress can take a while to show up. Voltage drop should be emntioned as well. The wiring in a Starion is pretty lite gauge. Double the current double the voltage drop to the coil. Now the cil is operating on less voltage. This system could easily hurt more than help. Since when did performance ignition coils beceme out of reach for the average guy? Â $40 dollars is not a lot of money. Â Most older cars need a new coil since the insulator tends to break down with age... Buy one good coil and your done. Also what type of meter are you using and whre do you have it connected up? Â Do you have any scope shots or test data to support your claims? Â How about a link to some testing? Can you quote some numbers from your meter? Including a comparison to a stock and or a performance coil. Â I would like to believe.... Â but i need a reason that a bit better than "cause I said so" DONT expect people not to question unsubstantiated, dubious claims! Â Thats silly... Â we are trying to not be sheep! If you have something that is not mainstream ... a little hard to believe you need to provide some substationation that it works. Kevin C -
Double coil ignition systems
TurboRaider replied to star_power's topic in Engine and Performance Mods
Well...... The only effect I can see is as the field collapses on the second coil it might help induce a/ more voltage on the coil that is connected to the dist. As any ignition coils field colapses a 400 to 500 volt spike is generated on the primary. Since the primaryies are connceted...... however the first coil will have a similar pulse, just slighly smaller since some energy was sent down the plug wire. It seems a like a hard way to get more spark since the blocked off coil is not even in the magnetic circuit. It is much more efficiant to just get a better wound coil. Also the current draw on the spark box is now doubled, that is likely to hurt the spark box. Most of the doubled current is being thrown away. Personaly I would recomend a better coil and or an MSD unit. Kevin C -
fooling the ecu into giving more fuel
TurboRaider replied to star_power's topic in Engine and Performance Mods
The alternator is not tied into the engine temp on the Starion system.... However I think there is a bit of extra advance when cold (and no EGR). Yes , fooling the engine temp sensor can add a few extra varaibles. Another way would be to fool the temp sensor in the Mass air flow meter. If you tell it the air is colder you will get more fuel. You could also try and find a higher pressure point to referance the fuel pressure regulator. If you had higher pressure than at the throttle body ... Like before the intercooler you would get a bit more fuel. Be careful though... Make sure you are going richer and the place you connect to has higher pressure. If your system is stock and you are not leaning out extra fuel may just get you running slower. Kevin C -
Check this out! I Need the Mut-II scan tool
TurboRaider replied to SiG's topic in Engine and Performance Mods
Mike, Very happy to see some real tech discussion! My ECU is an 88. The transistor that I ohmed out that pin 21 connectors to is labled Q4.  I have a jpg of the ECU that I can send you a tonight ...  I will mark it up with my interperation of the circuit. The picture given in the book for the pin and function for the connector to the ECU shows the cable side of the connector so you have to flip the pin and functions on the diagram to find pin 21. Pin 21 does not go to the thick film hybrid (as would be the case if the image in manual was for the ECU connector and not the cable). As far as q4 goes......  the 470 Ù is a wire wound (looks to be around 1/4 watt).  The 10 k is a ceramic and is 1/8 watt. Q4 is not the typical transistor as far as its pin and function.  The center pin is the collector.  This had me fooled for a while.  Pin 3 is the base leaving the power connected to the emmiter (pin1).  It does appear to be a standard PNP. The also is a 10k across the emmiter and the base on mine.  This base is connected to an IC labeled 647000.  The manf of the IC is Mitsubishi. I also noticed when checking the circuit out that the trace from the 470 Ù resistor to the transistor that the run goes under a component and is hard to find where it goes....  I pulled the PCB off the the base and verified it by looking at the back side of of the board.  The run crosses over to the other side of the PCB (side with the other connector). I feel pretty confident that I did not make any mistakes on this, however it would be great for not to just take my word for it and verify my fidings. Also there is the remote chance that not all ECU's were the same in the same model year. The best way to test a hypothises is through indepentent verification. Best Regards, Kevin C -
Advertised Duration vs. @.050???
TurboRaider replied to Tim_C.'s topic in Engine and Performance Mods
Agreed.....Selling at an advertised duration of .002 is a gimick... However there is a real reason for the slow take up ramps... it keeps the valve train from hammering tiself to death. Sounds like you have been measuring some cams with an indicator and a degree wheel? Kevin C -
Check this out! I Need the Mut-II scan tool
TurboRaider replied to SiG's topic in Engine and Performance Mods
Ok, I'm just not that good at teasing people... even if think they dissed me... :'( Besides I was right, internaly pin 21 on the ECU connects to the collector of a PNP type transistor. Â There is a 470 ohm buffer resistor beetween the pin and the transistor to prevent damage if the output is shorted. Â There is also a 10 K resistor from the pin to ground. The base connection of a PNP is output only..... Â You cannot send a serial signal through it. Â This is a ONE way comunications port. Â in non tech terms.... You would have better results pissing up a rope. Kevin C -
Yes, there is.... However I have a mill but no welder.... So that was how I made it. Kevin C
-
http://www.geocities.com/spun_bearing/windage_tray.html This is what I made for my Turbo Raider. I hope this helps, Kevin C
-
Check this out! I Need the Mut-II scan tool
TurboRaider replied to SiG's topic in Engine and Performance Mods
Mike, just to be clear.... I have not tried the MUT-II. My advice is based on my understanding of the 88-89 Mitsubishi fuel injection system. I have installed severl of these doing turbo swaps so I have read up on them as well as worked with them. I have spent a fair amount of time with a scope hooked up to mine (and others) to make sure it was working right as well as trouble shoot it. I have also worked in the auto industry doing electronic desing, so I have always kept an eye out for what was going on. Currnetly I work in electronics doing work that is similar to what you do (serial comunication and buiding test equipment) but for industrial applications. I work with a bus standard called ENDAT as well as a couple of propietary buses including one that I developed. Based on that experiance I beleive that the diagnostic pin on the ECU used on a Starion is very limited in capability. My belief is that this setup is similar to early ABS systems that could only be tested with a breakout box. I have opened the factoy ECU and I remember seeing a transistor to the test pin output. I will double check that tonight. Trust me I was not trying to stomp on anyones parrade.... Just offer some advice based on experaince. You are more than welcome to prove me wrong!!!!!!!! Best Regard, Kevin C -
Check this out! I Need the Mut-II scan tool
TurboRaider replied to SiG's topic in Engine and Performance Mods
How about dont shoot the messanger? I am providing good information about the system to the best of my knowledge. This was not and is not about whos knows best. I was trying to do the man a favor by pointing out that the older mits system does not support what he was trying to do. How about a thank you for taking the time to try and help us out? Or that I was willing to provide other methods to do the same thing? I have been working on a system that provides that same info but connects like the factory test box did. I am willing to share my ideas and approach to designing a test system. As far as pretending to know better.... Just because I have a differant opinion and engauge in a debate thats pretending to know better? The idea of a debate is to reach a conclusion, that is hopfully correct. I think your post and comments to me are way out of line. Kevin C -
Check this out! I Need the Mut-II scan tool
TurboRaider replied to SiG's topic in Engine and Performance Mods
Mike, As far as I know the one pin on the Starion only presents error codes on its one pin..... Yes those codes are presented in a serial form, but that is the only data availible on that pin. It's single direction port... there is no way to signel the ECU through that port to tell it to do something differnt. The manual shows it as a transistor driving an output line. I dont see any nice half duplux transciever on the ECU for a single wire interface. I am familier with serial interfaces, I just finished writing an interface spec for a customer. Why would I want to spend money when the ECU has it built in? If the information is readily avialible it seems using the ECU is a good way to process it. Again I dont know of a readily availible port from where to get it. Also I plan on adding other functions to my design so regardless I wold have a microcontroller. As far as hardware design goes... Microchips line of micro controllers need very little external hardware support, the cost is minimal to implement them. I have done several designs for uder $100 including an LCD. Wrinting the code is the biggest part, hardware desing is trivial (its also my full time job at work). Kevin C Design Engineer Somewhere in CA Some Small electronics Company -
Check this out! I Need the Mut-II scan tool
TurboRaider replied to SiG's topic in Engine and Performance Mods
Reality check time... The diagnostic connector on a starion only has one pin and that give ECU codes, thats all you are going to get from there. OK... If you use the equivilant of a breakout box you can monitor the ECU inputs and provide plenty of info for a test box.... But you need to get to the main connectors. As fas as the cost of an A to D.. There are decent microcontrollers with A to D's for around $10, not too expensive. Kevin C -
Sat down talked w/ machinist RE: 4K drop off
TurboRaider replied to Joel's topic in MPI/Standalone Trials and Tribulations
Exactly..... Yes. The cam sounds a bit small for the RPM range... Kevin C -
Sat down talked w/ machinist RE: 4K drop off
TurboRaider replied to Joel's topic in MPI/Standalone Trials and Tribulations
You feel the acceleration of the vehicle.... Â acceleration is dependant on the force applied and the weight. Â What you are saying is that you need your power in a usable range, compatible with the vehicles gearing system. The force applied is a funtion of RPM and torque. Â They are interrelated, one without the other means no power and no acceleration. Â This is simple math and a very simple equation. Â Yes a usable power band is needed. Â If your gearing does not match you cant get to the power. Â The real key is area under the curve, average power beetween shift points. Â Maximum area under the curve give the best performance. Â This can be had at any RPM band. Â Double the RPM, half the torque and get the right gearing and the accelreration will be the same (if power band has the length). Â The only differance will be if the inertia losses are higher in the high RPM engine. It would be reasonalble to assume the a 10,000 rpm screamer would have less inertia. For some real fun study what happens to power at the wheel at time = 0. Â By definition since the RPM is zero you need infinite torque to generate any power. There is an interesting bramch of math dealing with this called Laplace transforms. My real world example is again my old Duster.... Â Lots of high RPM power, I killed the bottem end and a good part of the mid range. Â Why was it good? Â I used a Richmond five speed with NO over drive, just four reduction gears and a 1 to 1 fifth. The faster car will be the one with more average hp as defined by its peak power and how close it shift points are. Â Again the one with the most area under the curve. As you knew.... Â you have to have the gearing to be able to use it. Kevin C -
Sat down talked w/ machinist RE: 4K drop off
TurboRaider replied to Joel's topic in MPI/Standalone Trials and Tribulations
Mike, My 2 cents on cams..... Â The cam sets the basic personaltiy of the motor. Â It determins the power range it will run in and where peak torque will occur. Â IF you drop the boost to just a couple of PSI and do a dyno run it should follow a very similar curve as when the motor is under 15 psi boost. Where you run out of steam under boost is the same as without. Fuel is the major limiting factor in making power... Â specificly detonation resistance. You can lower your compression ratio to allow more boost.... Â The idea is a longer slower burn, making power through a longer period. You do hit diminishing returns and at 4000 rpm you will get to a point where you cant up the cylinder pressure much more without detonation or changing the tuning to the point where each extra psi of boost does not contribute nearly as much to generate power. the other alternitive is to spin the motor faster. Â Get more power pulses at a lower pressure to do more work. As RPM increases for both a NA motor and a turbo there is less time to fill the cyl. Â This is why cylinder pressure drops at RPM as does torque..... Â but since you are turning faster you generate more power even though the pulses are smaller. The power curvewill follow the cam... Â a dyno tst at low boost should show the natural curve. Â It at high boost it falls on its face look for other problems like fuel delivery, exhaust restriction ect. Cam tuning can get you a few HP. Advancing the cam retarding it and noting how the motor responds can help tell you what way to go for your next grind. Â Dont expect a miricle though. If you want to make good power above 6300 RPM you need a bit of cam.... Â one that wont idle very well and is a dog at low RPM. Â Kevin C -
Sat down talked w/ machinist RE: 4K drop off
TurboRaider replied to Joel's topic in MPI/Standalone Trials and Tribulations
Nice work chip.... One thing I will say is that while Torque is what you feel right out... HP gets you back in your seat when you get going. I had a duster with a 420+ hp rever of a motor.... If you let that thing sing on the highway at 6500 rpm it would flatten you against your seat. .... HP is the work being done,,,,, Accelerating the mass of the vehicle. Kevin C -
Sat down talked w/ machinist RE: 4K drop off
TurboRaider replied to Joel's topic in MPI/Standalone Trials and Tribulations
An adjustable cam sprocket is easy to make....  Drill out your cam sprocket out for an offset bushing. The bushings are easy to make on a lathe.  Also 20º off on the cam?  No way in this world you are off that much.  Do the math, take the amount cut of the deck and the head and add them up. Take the Diameter of the cam sprocket mult it by 3.14.  Divide 360 degrees by the circumferance of the sprocket. Here is a wag at it....... {360º/ sprocket diameter *3.14}* amount you cut off your head = degrees the cam is off. example: 360 / 4.5*3.14= 25.53 degrees per inch of head removed....  To get off by 20º you need to cut your head a whole lot! Ok...  say you cut the head and the block a total of.08"  your cam would be off 25.53*.08= 2º. Your rapid torqu increase is due to the cam hitting its power band (normaly asperated same as all motors) and the turbo spooling up. Torque drop off is when you have a constant boost but less time to fill the cylinders.  A longer event cam helps....  more pressure helps.  what you amy want to ask is why is the torque dropping off faster than I like?  Horse power is a funtion of rpm and torque so as long as the torqu does not drop off too fast as the RPm inc you get more power. So what might hold you back?  All the things you ahve looked at..  noting new that I know of.  More intake valve area to reduce the pressure drop across the intake. A larger exhaust housing to reduce back pressure (AR ratio).  Drop the CR to get you out of detonation and pump up the pressure. Do some math for mass air flow..  To see if your numbers make sense.  Kevin C