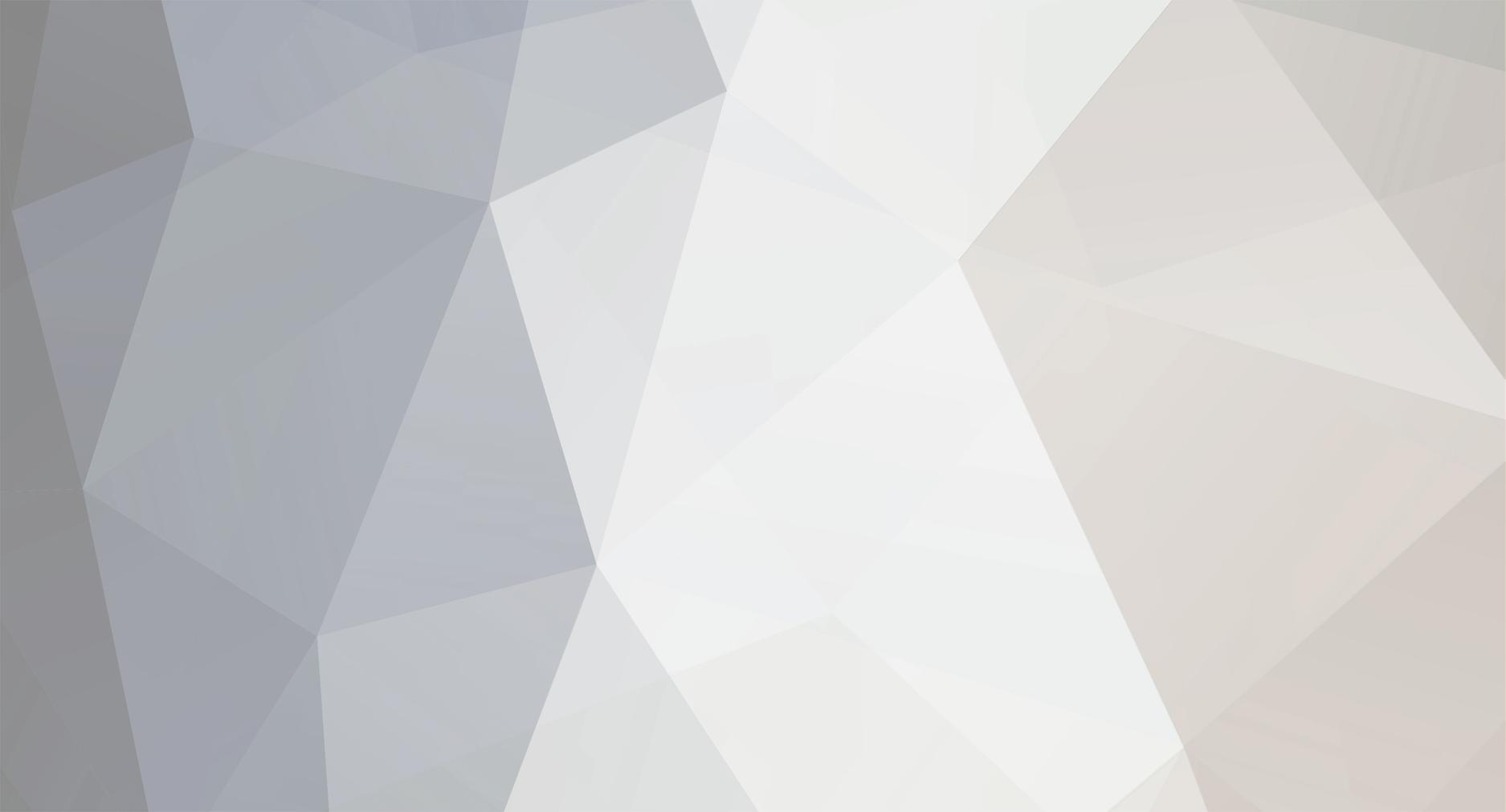
TsTKl
Members-
Posts
375 -
Joined
-
Last visited
Profile Information
-
Location
The Bay, Ca
-
Gender
Male
Contact Methods
-
ICQ
0
-
Website URL
http://
-
AIM
tstkl
Previous Fields
-
Model
Conquest
-
Type
TSI
-
Model Year
1988
-
Transmission Type
Manual
-
Interior Color
Black
-
Status
Restoring
TsTKl's Achievements
Newbie (1/14)
1
Reputation
-
The product is pretty old, LC-1, probably in 2006 or 2007 when they first came out, maybe earlier, but I asked them how much it would cost to fix it and they stopped responding. I approached them at SEMA and said, "the lc-1 is a piece of crap, just buy a lc-2". Oh yeah, sure thing.... Also this is the second time it broke. They already "fixed it" once. Also I am aware of their software F-up. https://www.ecmtuning.com/wiki/innovatelc1orlm1install "Version Check: Please take note of the version of LM Programmer shown in the screenshots. There are newer versions (v3.19 and 3.27) that are shipping with the units that Innovate knows does not function as it should. For some reason, they do not mention this anywhere." Thanks, the intercooler is a dead brand, I'll replace it one day but the pipes are super low volume. "Johnny Racecar" for those who remember.
-
This website is almost unusable, can we get these issues fixed? I can't even get the quote feature to work, let alone the multiquote feature. Typing is also horrible. Anyways, in response to your suggestion, please remember, this is ME you are talking about. Redundancy is my middle name. http://s81.photobucket.com/albums/j223/tstkl/conquest/motor/2015-03-30%2019.26.43_zps6sjmhdg4.jpg It is hard to see, but there is already a second o2 sensor bug in the exhaust. There are plenty of people who have ran these sensors how I am, but if needed, I can make changes. That is also currently a narrowband o2 sensor because innovate sucks and refuses to fix my lc-1.
-
So, sorry this is a day late, but the powder coaters took an extra day with the parts I was getting done (no no chi, thorough is good). Anyways, I’ve done a lot of small steps since I last posted on here, I’m sure I’ll forget a lot. The biggest thing for me was getting the cams degreed. I bought a 9 inch degree wheel because effectively I was trying to find a basket filler from a specific website and 9 inches was the largest they had. It actually turned out to be really good as it would have hit more things if I had bought a larger wheel. I was able to use some plumbers tape as an indicator, and mount it easily to the bolt holes in the water pump. The biggest challenge was not having solid lifters. I would highly recommend anyone who is degreeing their cams use solid lifters. I ended up making a spreadsheet and measuring the displacement of the valve and the lifter to find the cam’s position relative to the crank. Exhaust was 8 degrees off, intake was 4. http://s81.photobucket.com/albums/j223/tstkl/conquest/motor/2015-03-13%2019.49.36_zpsu4io9ah4.jpg The most noticeable thing was the intercooler piping and intercooler. The radiator still isn’t bolted down up top, but the intercooler is fairly secure. I was able to weld together the intercooler support bracket, intercooler piping, and intake pipe. The blow off valve will recirculate for now, and the car is fully capable of being run in speed density or standard maf style. This is all “finished” except the intake pipe will eventually be replaced for a larger diameter. http://s81.photobucket.com/albums/j223/tstkl/conquest/motor/2015-03-17%2019.03.29_zpsa6rx1bcu.jpg You’ll notice a lot of other stuff from this picture. I was able to paint the valve cover how I wanted it pretty successfully. It is a black base coat with a green metallic “over spray” and a clear coat over that, all spray painted. I’m expecting the paint to melt off when I get the car running unfortunately, but it looks pretty good for now. Also, you’ll notice the catch can in the back corner. I welded that together myself. It has a special feature that I want to test out. There are three ports on it for the engine. Two on the valve cover and one off the dip stick. The idea is any pressure that builds up in the crank case will go out the dip stick first hopefully. I was also able to get some smaller stuff done. http://s81.photobucket.com/albums/j223/tstkl/conquest/motor/2015-03-17%2019.03.37_zpsmjl2kzbr.jpg Here you can see the “upper” intercooler pipe and bov recirculation tube. The inline thermostat is a work in progress, but you get the idea. The coolant system is very very close to being done, which is great because it has been a fairly large pain up to now. The coil pack mount is also temporary, in the sense that I will convert to coil on plug eventually, although I do very much like the idea of keeping this arrangement, as I have 7 (yes 7) spare oem coil packs somehow. http://s81.photobucket.com/albums/j223/tstkl/conquest/motor/2015-03-17%2019.03.43_zpsim6o0hpp.jpg The “lower” intercooler pipe can be seen here, as well as some other finer details. The green from the valve cover can really be seen here. The idea is, in low lighting the valve cover looks 100% black, but with light the green can be seen. I got the idea from the 2004 STI oem paint, “java black pearl” which uses gold instead of green. http://s81.photobucket.com/albums/j223/tstkl/conquest/motor/2015-03-17%2019.04.30_zps27egolvw.jpg Here you can see the o2 sensor heat sink. Wideband o2 sensors generally don’t like the heat of a turbo, so I made this as a modified version of this idea: http://www.ecmtuning.com/wiki/innovatelc1orlm1install I had the aluminum sheet lying around, as well as the aluminum heat sinks. One look at my company’s welder and it was done. You can also see the clutch system bleeder on the firewall. The original plan was to have it on top of the backside of the transmission so I could perform bleeds from inside the car and thus only need one person, but the shape of the transmission and trans tunnel made that difficult, and honestly, this was too easy to do this way. I know a lot of people have trouble properly bleeding this style slave cylinder, so having a nearly vertical line seemed logical. It should be noted that I am still not happy with the wiring. I am going to re-loom the engine wiring harness, and possibly the chassis wiring harness as well. I plan to get a decent amount done this week as well, as I don’t start my new job until next Monday. I do not have a welder anymore however. I think I will be filling the car up with oil tomorrow and running the oil pump, although that will more so be to check the volume of the oil system with the large oil cooler and such installed. I have a list of just under 40 things I still want to do before firing the car up, so it will still be a while, but it is nice to see so much progress again. Also, those 40 things does not include “put a steering rack in the car”, so even once it is done the car would only be able to theoretically drive forwards and backwards, and wouldn’t be able to turn. I’m pretty concerned about properly braking in the motor, so I’m not too keen on starting it up until everything is perfect. Also that is the largest driving force behind the maf/speed density redundancies. P.S. I'll try and fix the pictures tomorrow.
-
I'm not going to lie, a lot of the motivation I currently have for working on this project comes from people constantly sending me links to (numerous different) articles about lazorack's car. I'm changing jobs again, so I should have more money for this project, although less access to a certain welder, mill, and lathe unfortunately. Will have a quality update in 11 days. Promise.
-
Hey guys, Just wanted to let you know that I've started working on this project again and should have some progress to post soon.
-
recently moved to LA, totally down.
-
would you guys be willing to send me any of the files you've created? especially anything solidworks or suspension related. I really want to fix the rear end of this car so the more accurate the better. Also, I never realized how angled the shocks are from the factory, I might have to design a double wishbone subframe for my car.
-
Fidanza LT1 flywheel for Bills T56 bellhousing
TsTKl replied to AustinTSI's topic in Transmission Swaps
Hey Guys, I didn't take the time to read this entire thread because I've seen it a million times. Here are some facts I've collected on the subject: 1. The ONLY LT1 or LS1 swaps I have seen that didn't involve cutting the transmission tunnel had the engine significantly lower in the engine bay than what is found from the factory. 2. The automatic transmission chassis have larger transmissions, and thus larger transmission tunnels, so certain applications where an auto car was used can unknowingly "skew" results. 3. The oem transmission is not tapered past the bell housing whatsoever, and the oem tunnel reflects this. Similarly, the ls1/lt1 transmission is not tapered, only the bell housing is. Moving the transmission forward an inch wouldn't do s*** to allow it to fit better. It still wouldn't fit. Period. Moving it DOWN an inch would help a ton. 4. The lt1 bell housing is an inch shorter. The bolt pattern is also offset about 17 degrees from the ls1 transmission. I have the second bell housing from Bill I believe. It was designed for an lt1 and then elongated for my transmission. The transmission mount doesn't line up with the body of the car and the shifter is pointed away from the driver. I will be getting a new version from bill once I have the money and confirm with bill that the changes I need have been made. (lack of time and funds on my part as it sounds like Bill has finished this project) 5. I am extremely sick and tired of hearing people say that these things fit in these cars. They don't. Honestly it cost me over 1000 dollars in logistical f*** ups listening to people over the internet saying it would fit, only to find out at a very very inopportune time (I was moving) that it doesn't and the couple days I had budgeted for putting this car together and shipping it wasn't going to work out. STOP SAYING SOMETHING WORKS UNTIL YOU TRY IT. All that being said I do appreciate that people are trying to "pave the way" for others. -
Hey guys, thanks for the compliments. I think about this project probably every day but my current financial/living situation is preventing me from making significant progress. The car is in storage and I can't really work on it, but I've got some solid ideas down on paper that should work out really well. Also my new job has a welder so I'm getting a lot of the little welding projects I needed to get done finished. Hopefully there will be an update at the end of next month of some significance.
-
design it in cad and pay someone who already makes swaybars to bend it for me was my game plan, however I just got a job at whiteline flatout, so I'll probably have an easier time making it now.
-
the good thing about the t-56 though is that it has such a large aftermarket. That's what lured me to it, because the 4g63 is the same way. I believe ppg makes a dogbox kit for it I plan on installing someday.
-
Nor Cal Spring 2014 Swap Meet and BBQ with Dave Wolin
TsTKl replied to Scotty Dont's topic in StarQuest Meet Planner
interested, I just accepted a job in LA but if its on the weekend I can possibly make it. -
most accurate post in this thread /\ just to clarify: the engine designation has nothing to do with narrow/wide or RWD/AWD/FWD. For US 2.0 what kane said is all that matters: Mighty Max, D50, Ram50. 2.0L (engine code g63b) Automatic only. Measure lower bellhousing bolts to be sure, 13.25 inches center to center. for 2.4 liter engines there are some vans etc you can find.
-
still available
-
No big deal,.... now he will just have his LCA in compression instead of tension under braking, LOL. Working and working well are two different things hahaha