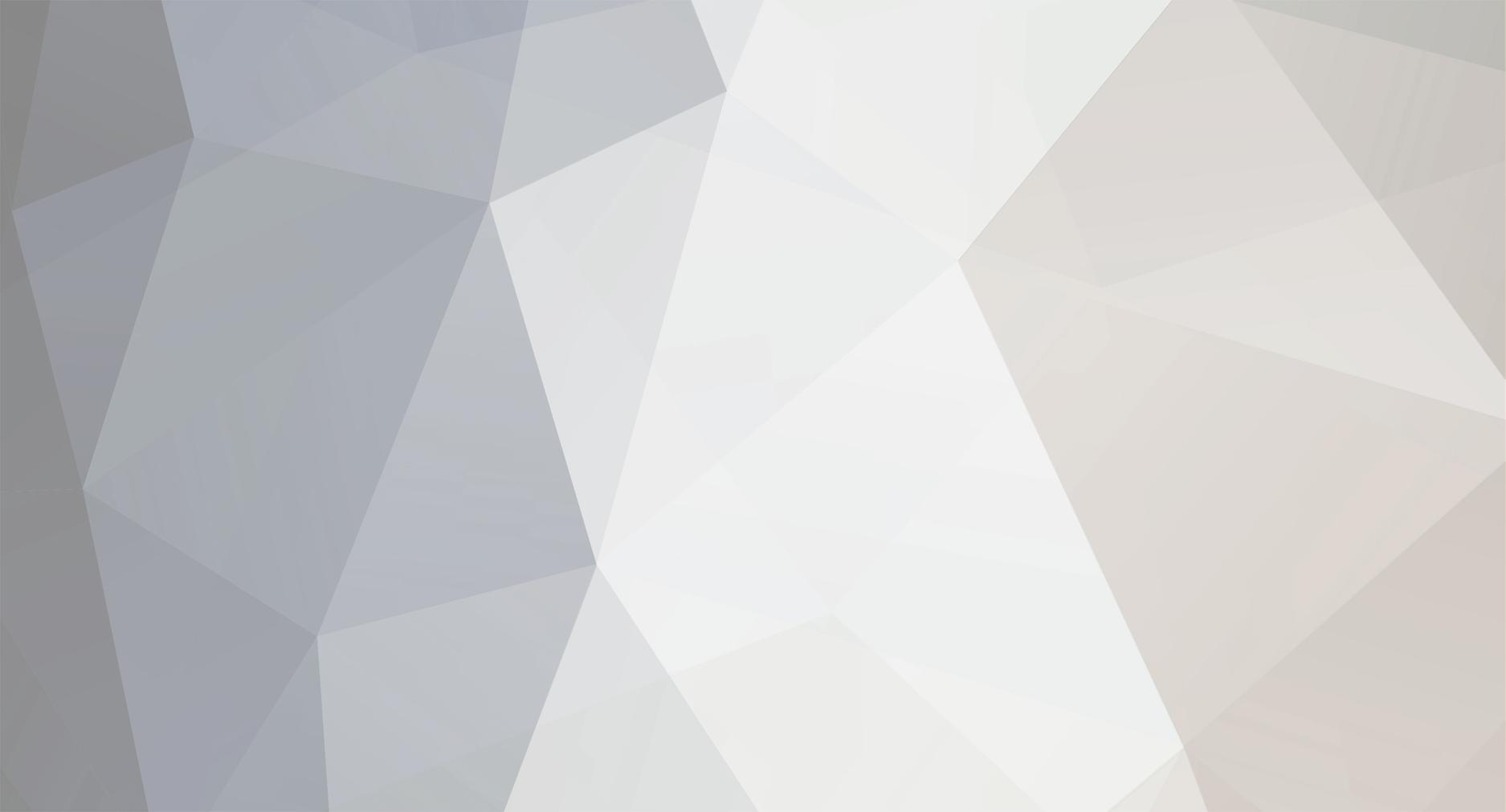
TurboRaider
Members-
Posts
153 -
Joined
-
Last visited
-
Days Won
1
Content Type
Profiles
Forums
Calendar
Gallery
Everything posted by TurboRaider
-
3.90 and 4.22 gear set up
TurboRaider replied to StarquestRescue's topic in Advanced Virtual Mechanic
Two tricks come to mind for diff setup. One is to use a spare set of bearings for the setup that have been honed out and hopfully match in height to the bearings you will use for final assembly. You can use a spare polished down pinion shaft that slip fits both of them and compare them in the diff housing to be sure they match. This trick works really well. That will get you very close on gear setups, as with any gear setup that last few tenths are hard to get just right. The other method I use is to polish down the pinion that I will be using to have a very tight slip fit. I set up the diff that way get the shims just right and then use Loctite stud and bearing mount for final assembly. Its never failed me in 20 + years, although you need to use heat and a press if you ever try to take the pinion apart. Make sure you use cleaner on the parts for final assembly as well as the Loctite primer. Also on hard to set up gears where the factory shims selection is either too tall or the next shim is too thin I will take a few tenths off the tall shim using a surface plate and a piece of 600 grit abrasive paper. I set up some very used 4.62 gears with 340,000 miles and they crown on the gear teeth was worn enough that a tiny change in the pinion height moved the pattern a lot. Sure new gears would be nice but.... I set the pattern up slighly inboard so it centered under load and they are nice and quite. Tiny bit of noise under coast but I expected that when I moved the drive pattern. They are way better that how they were before I set re-set them up. Kevin C -
Throttle body /Magna intake Hybrid
TurboRaider replied to macrophage's topic in Advanced Virtual Mechanic
The tuned RPM for a runner in a manifold changes as the boost pressure rises. More pressure raises the speed of the reflections and lowers the tuned RPM. Basicly a tuned manifold is hard to use under boost since the tuned RPM varies with boost pressure. Why did I just buy one? The long runner manifold is great for off throttle response before the turbo starts assisting. Since most turbo's dont do a whole lot till at least 2800 RPM and as you add a bigger cam you lose throttle response this is a great way to improve low end torque. Also fuel economy when in the tuned rpm of the manifold will be better, so for general cruise this is an advantage. My theory is to tune the intake for low RPM pre boost driving with all four runners tuned to that RPM range. To me it looks like the Magna is a prefect choice. Since pre boost air flow is now greater the turbo will spool faster. Add that to the obvious advantage of better fuel distribution. I'm also curious to see how much adding a by pass valve will help fuel economy since it prevents boost at part throttle / low load conditions. The more I opened up the exhaust the more boost I see above the throttle under cruise. I would be curious to see if that is knocking back my ignition timing at all. Soon to have a M7 head and MPI intake:) Also I will be looking at using the rear water port inthe head to see if I can get a better temperature gradiant across the head. Kevin C . -
The only turbo that does not have shaft play is one thats siezed :rolleye0018: That said... Each bushing needs at least .001 clearnace in the housing and the same to the turbo shaft. That allows the shaft to move +-.002 at each bushing. The end of the shaft overhangs the bushing at least quite a bit. Basicly if you measure how fat the tip of the shaft moves .01" ( +-.005:) total movement is not unusual. Bad is the impeller contacts the housing. Bad is a shaft or bearings with a lot of scoring or a housing that has wear grooves. If the housing is bad and you look closly you will see a wear ridge that ends near the snap rings. Kevin
-
On the subject of blowing smoke.... I would skip the TS rings. A thin steel top ring on a good forged piston will get you better performance, run the gap to the wide side on the second ring. Kevin
-
Alternative Source of Oil for Turbo
TurboRaider replied to Jayton's topic in Advanced Virtual Mechanic
I think you will find that if the O ring is bad or missing you still get good oil pressure but the oil that leaks past the O ring is not filtered. If two O rings were somehow stuffed in that cavity its possible that one of them could block the oil passage for the turbo feed. Kevin -
Shelby, What pissing contest? I was trying to understand your 3X faster claim. Perhaps I misunderstood it the first time. I thought you meant it could be over driven by the air flowing past it at high speed so it wont drag on the engine. What I think your saying is based on its internal design it can run faster than the input shaft speed to it (even if the vehicle was sitting still). Is that what your saying? Kevin
-
Quick calculation: Assuming your in gear at 60 MPH If a 24" fan was running 3X the engine speed and the engine is turning 3000 RPM the fan is running at 9000 rpm (according to the Shelby 3X theory). The tip speed of the fan would be (3.14 X 24"X 9000 RPM )/12" = Feet per min 56620 or 643 MPH. Since the blade is at an angle the air speed to drive it that fast will need to be adjusted by the tan of the angle. For a 25º angle as a wag divide the tip speed by 4 (inv tan). 643 /4= 158 MPH vehicle speed would be required to get the fan to run at 3x engine speed (assuming no slow down past the grill or the radiator and the engines at 3000 RPM). No way. Remember that the air speed through the radiator is lower than the vehicles air speed since there are a buch of restrictions in front of it. Running at 60 MPH, 3000 RPM At a fan speed of 3600 RPM (engine RPM x 1.2: pump RPM because of the pully ratio) the blade tip speed is 256 MPH. 256 /4 = 64 MPH! The fan would still want to pull the vehicle and not want to be back driven by air flow through the radiator that would be coming through the radiator at something less than 60 MPH ( like 35 MPH). My numbers may not be perfect but they get things in a reasonable range and show that the fan is not being back driven by air flow at some crazy speed. My theory falls apart if you can run at an idle while going 120 MPH :character0028: Funny stuff huh? Kevin
-
Shelby, What up with the "again an uninform'd person " comment? Do you have a link or any data to back up the claim that the fan can spin 3 or 4 times faster than the shaft its mounted on ( I assume that what you meant and not engine RPM)? Kevin C
-
I went to electric fans on my 2.6 Turbo Raider to get better low speed cooling. When (edit)- crawling- in gear with an auto the mechanical fan spins pretty slowly (edit) because the engine is turning slowly!!!!, and of course that is when you need the fan the most. (edit/ new) Since the electrics spin at full speed even when the engine is at an idle you get much better air flow when going slow. Before the electric fan mod I would get a nasty heat buildup under the hood when crawling. With the nose pointed up hill the heat just stayed in the engine compartment to the point that I boiled my battery!!! Most Starions dont have a 2.85 under drive crawl gear to allow super slow trail crawling so this is an extream example. But it is the same motor and it shows how cooling can be improved when engine speed is slow (auto tranny ideling in gear, sitting in traffic is a good example). Saving a few HP is a nice bonus to not overheating when going really slow in hot weather. Kevin C I added a few key words and expanded on the subject a bit... You can find the original in a quote by the grump old guy a bit further down.
-
The offset pins will also help to reduce piston slap when cold. The only down side is slightly higher friction. My preferance is to run the offset pins. Kevin C
-
Mopar Factory performance manual says the 2.6 head can take a cut of .040" if your need to increase your CR. I have run a few motors with the head cut .030" on my NA performance motors and .020" on the turbo motors and never had a problem. You want to pay attention to your cam timing and shim the plunger on the pump to limit its travel when you take a lot off the head. I have also built and long term tested 8.8 to 1 , 8 to 1 , and 7.75 to 1 CR turbo 2.6 motors, ion nitrided cranks, windage trays, deep valve retainers that allow longer springs for high lift cams, deep sump pans, improved crankcase breathing as well developed a hand full of other tricks. Some worked some didnt.... Cutting the head .020 was not an issue. It will raise your CR but on a 7 to 1 motor thats not a problem. Kevin
-
You can send a sample to a lab just to be sure that it does not have any coolant. Might try Blaackstone. Kevin C
-
The last .060" of the plug does not have any threads so no threads are exposed in the chamber, I dont think this is a real problem. I have been running that length plug in a Marnel head for 8 years and have not had any pre ignition issues. Kevin
-
http://www.starquestclub.com/forum/index.p...c=72107&hl= If you take 7 lbs off the crank and the effective distance from the axis of rotation is 5". 7 lbs = 3.2 kg 5" = .127 meters The moment of inertia of the weight removed is 3.2kg*(.127m^2) = 0.051 kg-m^2 Assuming 500 RPM per second engine acceleration: (kg-m^2/sec^2) = .051 kg-m^2 * 52.4 rad/sec^2 = 2.7 N-m or 2 lbs-ft of torque This is how much torque the mass would have taken away from accelerating the car if your changing the RPM at 500 RPM second. To put a HP # to that figure at 5000 RPM it would be: 2(5000/5252) = 1.98 hp Kevin C
-
Anyone ever tried a different timing chain?
TurboRaider replied to emagdnim's topic in Advanced Virtual Mechanic
What Shelby is refering to is inertia loading as the cam accelerates. IMHO its not an issue since the inertia loading is small compared to the force required to overcome the drag from the valve train. There are two reasons why its not a big factor: 1: The cam is accelerating at 1/2 the rate of the crankshaft, and 2: The cam is small in diameter so tis moment of inertia is small. Combine a small moment of inertia with low acceleration rate and you dont get a very large force. You can cut some weight out of your motor if you center drill the cam. Kevin C -
Fusable links should run hot at maximum load. Remember that on an overload they need to get hot enough to melt the wire, to get that hot they are undersized from the rest of the system, thats enough to get them hot during high loading. Kevin C .
-
Anyone ever tried a different timing chain?
TurboRaider replied to emagdnim's topic in Advanced Virtual Mechanic
The average torque required to turn the cam should fairly be constant over RPM. The power required to turn the cam goes up with RPM since power is a function of RPM and torque. The stretching load does not double becasue you go from 4000 to 8000 rpm, just the power to turn the cam. Basicly, the cam should not require more force to turn at 8000 rpm than at 9000 rpm. That said, a valve train setup the requires more spring pressure to prevent valve float at higher RPM would increase timing chain loads. As a referance point we have a double roller chain running a 4 cyl valve train. How does our chain compare to a SBC opening 2X the valves with a lot more sping pressure? Also if you have rollers rockers chain loading will be lower and as RPM goes up inertia helps even out the torque pulses. Nice to know you can get a custom part made, I would break a stock factory chain in (thats when the most change occurs), degree the cam and see how much the chain is moving on you over several runs. You might find that the factory part is very well built since it was designed to last at least 140,000 miles. If you decide to go forward an interesting test would be to cut one apart and have the shop tell you if they can do any better. Kevin C -
50,000 foot view... If the oil is getting so hot that its killing the turbo, I doubt the other bearings would be in very good shape and the oil annlysis would have shown that. Hot oil usually results in coking, sludge and short oil life, like 2000 miles: not 50. Having the oil at the right temp does help but this is to happening a bit too fast. Checking the oil T Stat is a good idea, however as other have pointed out (including myself) braided lines and hot turbo's are not a good mix. I learned this on the cooling lines, I hade a failure after two years when using high quaility AN type lines. IMHO its either a batch of bad turbos or oil starvation. Kevin C
-
IS there a MSD 6AL installation write up
TurboRaider replied to Sully's topic in Advanced Virtual Mechanic
My experience is that the more modified the engine the greater the benefit. On motors with a lot of cam where you get greater mixture dilution the MSD helped a lot as did a couple of other tuning tricks. As you get closer to stock the gains are smaller. Our little Hemi is known for slow combustion speed and stock has a reasonable amount of valve overlap. Stock its no race engine but it my experience it does respond to a stronger spark. The MSD uses capacitive discharge to drive the coil. Typically these systems have bit less total power per spark than a Kettering type systems but the rise time is a lot better. The faster rise time helps prevent misfire from fouled plugs. All plugs will look a bit fouled on startup until they come up to temp. On a turbo motor you run cold plugs to keep plug temps in range under boost. Basically the plugs are not running very hot under normal driving so insuring good ignition is harder, they stay cold longer and off boost are running colder than is optimal. That’s where a fast rise time spark can help. In general CD ignitions are not as good with lean mixtures, but a multi strike CD seems to get around that issue. Kevin C -
IS there a MSD 6AL installation write up
TurboRaider replied to Sully's topic in Advanced Virtual Mechanic
Same thing on mine and my fuel economy picked up a tiny bit... Spark plugs dont last very long though. Kevin C -
A hand held temp gun aimed at the oil pan is a quick way to verify your oil temps as well as into and out of the oil cooler. The oil thermostat is a good thing to keep. Cold oil builds up moisture causing acids and extra wear. Low oil temperatures lowers HP and creates extra friction. I have found that flex lines dont do well when connected close to the turbo. I really think a hard line is the best way to connect the last 8" to the turbo for both the water and the oil. Kevin C
-
I ran 8.7 truck pistons at 9 PSI boost for six years, 60,000 miles ... I did fail one from over reving it it developed a crack in the skirt. That one was a sealed power replacment, the factory 8.7's have stronger skirts. The crank size differance is true but a bit backwards... It sounds like somone read the direct connection manual for the 2.6 motor. The early blocks had a large main bearing (66 mm) in 79 and 1980 the 2.6 and 2.0 went to the same sized bearings as the Starion engines we currently work on ( 60 mm). Lots of turbo blocks were used in NA applications. They are not drilled for the oil jets but the knock sensor boss is there and drilled and tapped. The only sure way to know if you have oil jets is to drop the pan, unless you have a non turbo block with no boss for a knock sensor. I hope that makes sense.. Kevin C
-
I ran a test on a used set of ceramic coated pistons a while ago. I had two pistons one coated and the other uncoated. I put each piston over the same flame (one at a time) on my gas stove for one minute and then measured the temperature. Both the coated and the uncoated were within a degree of each other after 60 seconds in the flame. That makes sense since to be a good insulator a material needs to have a low thermal conductivity or be fairly thick. An ok conductor and thin does not make for a much of a change. Another way to reduce heat transfer is to change the color to a light color. Shiny silver piston tops will in theory reflect heat back better than a dark top. However an aluminum piston is shiny to start with and both the ceramic coated pistons and the non coated pistons have the same combustion color after the motor has been running for a few thousand miles. Coatings may help on manifolds where they can stay the same color but I'm not convinced they do a thing on pistons. Kevin
-
Last I checked you needed to go to .040 over if you wanted the narrow steel rings. The steel rings will take more heat , reduce friction and for a given size conduct heat 15% better than cast iron rings. That was why I went .040 over.... Kevin
-
Leanest / Hottest cylinder for EGT probe install
TurboRaider replied to Car6on14's topic in Advanced Virtual Mechanic
Why would # 4 be the hottest on a MPI? Usually the inboard cylinders from the end of a head run the hottest. The end cylinders have a natural heatsink... The metal at the end of the head. This is not a new idea and its backed up by the head usually cracking on cylinders 2 and 3. That rule holds true on carb motors as well as TBI and on three differant intake manifolds. Kevin