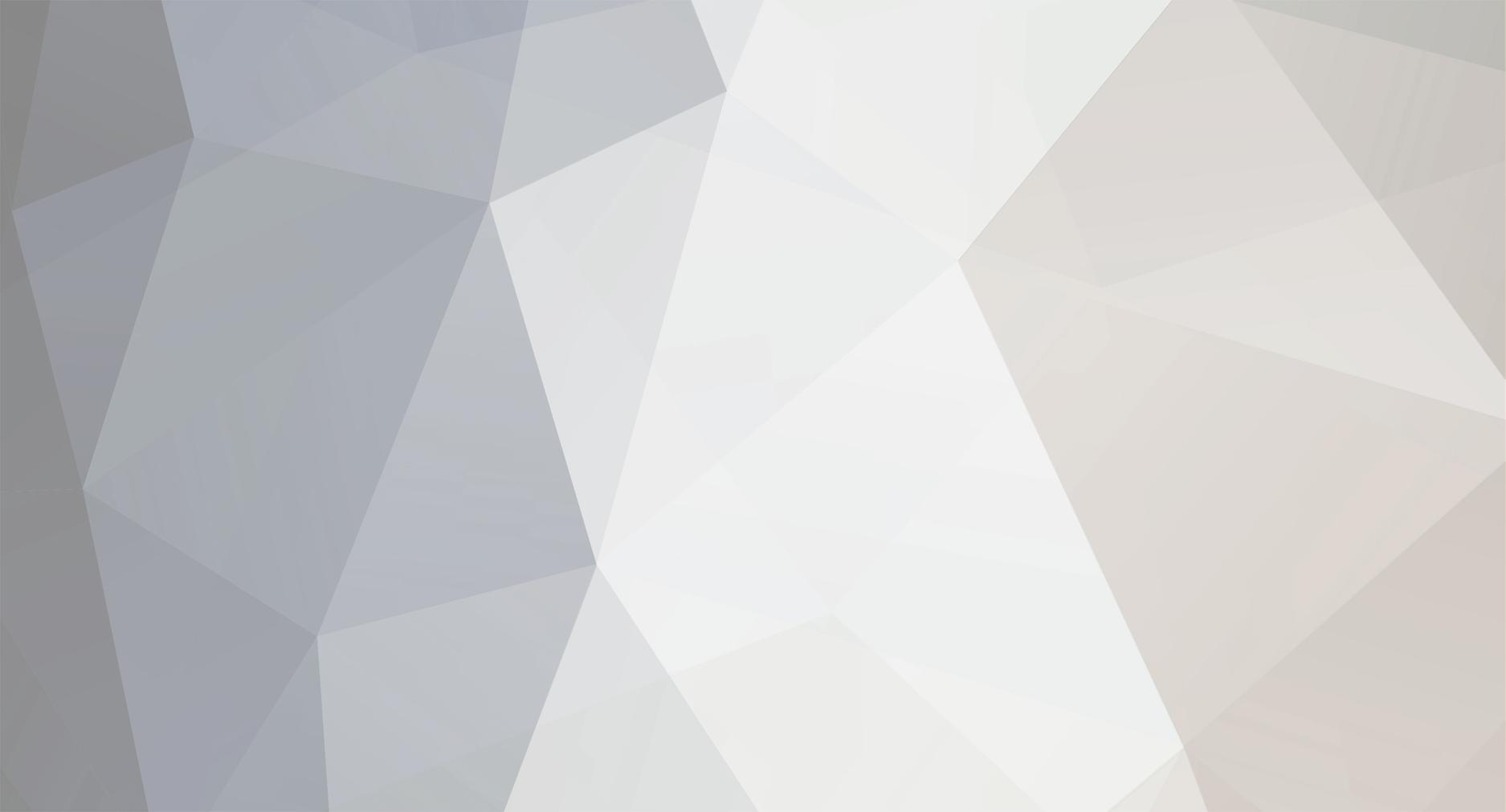
Whiplash
Members-
Posts
739 -
Joined
-
Last visited
Content Type
Profiles
Forums
Calendar
Gallery
Everything posted by Whiplash
-
I like the way you think!
-
I know this is an old post. But had to tell you guys that NAPA corp. never did contact me about this issue. And it would cost more to go to small claims court than the valves are worth. I haven't bought parts from NAPA since. AutoZone sells the same stuff as them anyways now at a lower price. Rumor is that AutoZone might start carrying brand X who's a much higher quality part that what NAPA sells. Note: corp owned stores sell the lower quality parts. Privately owned stores has always sold both brands.
-
FYI. Here's a good read on bearing analysis. http://www.engineparts.com/pubs_detail.asp?c=4&id=55
-
Just stopping in to say hi! I see things haven't changed much!
-
WOW, In reference to my spark plug thread
Whiplash replied to allen405's topic in Just plain ol' B.S.
I took out some NGK's that I had in my 4.7l Dodge and put in some E3's. E3's didn't seem to have the powerband the NGK's did. I noticed it from day one. Will stick with NGK's on ALL my engines from now on. Also no MPG gain as stated on box. Waste of money for E3's. -
If installing a NEW flat tappet cam it must be run for 30+ minutes at 2000-2500 rpm to seat it.
-
Wix found at NAPA and Carquest stores.
-
What he said, but back in the day the head gasket required re-torquing. True that most gaskets today don't require it. But depends on how thick the fire ring is in the head gasket. If installing a new camshaft you must break it in first at about 2000-2500 rpm for at least 30+ minutes with Zinc. additive. What type of rings? Chrome requires a HARD break in. Cast just baby it. Moly is in between.
-
Time for the 1st oil change. WHAT to put in it?
Whiplash replied to DurbenQuest's topic in Advanced Virtual Mechanic
Talking about a flat tappet cam ver a roller cam. http://www.aera.org/eptb/TB2333R.pdf -
X3
-
I have heard that over 50% of engine issues are with media in the engine. I know of one machine shop that cleans the engines in a different building, and than moves the engine parts to a "clean room" to be put together. After the customer picked up the engine it failed. In analysis of the engine components it showed signs of silicon (sand). BTW the engine machine shop was so clean you could eat off the floor. Well found out that the customers truck had a little sand in the bed. It's believed that the wind picked up some of the sand and blew it into the engine. Point is clean your engine well and keep a bag around it until it's completely sealed.
-
Dana still owns the OEM division of Wix, but not the aftermarket div. Did you guys know that Wix makes most of all the OEM filters that is on your engines when new. When someone states that the OEM filter is better than all others he really means that Wix is better, he maybe didn't know it. I've seen many studies over the last 25 years about oil filters. And Wix has the best bang for the buck. They include the anti-drain back valve, by-pass valve, and several other positive points. So when you run down to buy an OEM Ford, Chrysler, or GM filter you're buying a Wix. Worldwide Wix is used more that all other filters if you include the OEM div. and aftermarket div. together. Fram is only aftermarket sales. It's just that Fram puts more money into adverts.
-
the cars that you have owned and miss
Whiplash replied to jspecgallant's topic in Just plain ol' B.S.
1968 Jaguar-Damiler 250 V8 1987 Shelby Charger. -
All oils including Rotella has removed the zinc and other additives in their oils in Jan 2007. Ref http://www.aera.org/eptb/TB2333R.pdf
-
The red stuff is what you put on the cam, etc.. to let it have some lubricant until oil gets to the journals and lobes. ZDDP is a second additive that has some zinc and other stuff to help harden the metal. If the zinc additive isn't added it can wear the lobes in mins. And more issues within 1000 miles.
-
MISFIRING IN SEVERAL CYLINDERS Checking the Compression Remove all spark plugs. Carry out a compression test. If the compression is OK : Check the cooling system. If the compression is uneven : Rectify as necessary, then replace all spark plugs. Checking the Cooling System Connect pressure tester P/N 9985496 to the expansion tank. Pump up a pressure of approx. 100 kPa (14.5 psi) . Shine a flashlight into each cylinder and check that there is no leakage between the cooling system and cylinders. If there is no leakage : Check the ignition leads. If there is a leak : Rectify as necessary, then replace all the spark plugs. Checking the Ignition Leads Remove all the ignition leads. Check the ignition leads for signs of damage, cracks and flashover. Then measure the resistance in each ignition lead. Resistance should be 1.5 - 4.5K ohms depending on length, at +2O°C (68°F ). Replace all ignition leads which are damaged or have incorrect resistance. Check that there is no loose connection between the ignition leads and distributor cap, ignition leads and spark plugs and between the ignition lead and coil. Rectify as necessary. Then continue with: Checking the distributor cap and rotor. Checking the Distributor Cap and Rotor Remove the distributor cap. Check the distributor cap/rotor for signs of damage, cracks and flashover. If a fault is suspected: Clean, if necessary replace those parts which may be damaged. Then continue with: Checking the ignition coil's primary winding. Checking the Ignition Coil's Primary Winding Switch Ignition OFF. Disconnect the cable terminal from ignition coil connector 15. Connect an ohmmeter between the primary winding's two connectors (1 and 15). The ohmmeter should show 0.5 - 1.5 ohms at +2O°C (68°F) . If reading is OK : Check the ignition coil's secondary winding. If reading is incorrect : Test with a new ignition coil. Then continue with: Checking the voltage drop. Checking the Ignition Coil's Secondary Winding Switch Ignition OFF. Disconnect the ignition coil's high-tension lead. Connect an ohmmeter between connector 15 and the high-tension connector on the ignition coil. The ohmmeter should show 8 - 9K ohms at +2O°C (68°F) . If reading is OK : Check the voltage drop. If reading is incorrect : Test with a new ignition coil. Then continue with: Checking the voltage drop. Checking the Voltage Drop Fit new spark plugs. Install the distributor cap and connect all ignition leads. Connect the cable terminal to the ignition coil. START the engine and let it run at idling speed. Connect a voltmeter between ignition coil connector 15 and ground. The voltmeter should show battery voltage . If reading is OK : Check the power stage ground connector. If reading is incorrect : Check the voltage supply connectors at the junction box, relay 2/31 and battery positive terminal for signs of loose connection, contact resistance and oxidation. Then continue with: Checking the power stage ground connector. Checking the Power Stage Ground Connector Switch Ignition OFF. Wait for about 150 seconds. Disconnect the power stage. Connect an ohmmeter between power stage connector 1 and ground. The ohmmeter should show approx. 0 ohms . If reading is OK : Check the power stage leads and connectors. If reading is incorrect : Check the power stage ground connector 31/52 for signs of contact resistance and oxidation. Then continue with: Checking the power stage leads and connectors. Checking the Power Stage Leads and Connectors Check the leads between the following components for signs of an intermittent break, intermittent short circuiting to ground and intermittent short circuiting to voltage supply: Power stage connector 4 and ECM B11. Power stage connector 1 and ground connection 31/52. Power stage connector 3 and battery positive terminal. Check also the following connectors for signs of loose connection, contact resistance and oxidation: Power stage. ECM. Electrical distribution unit. Relay 2/31. Battery positive terminal. Ground connection 31/52. Rectify as necessary. Then continue with: Checking the flywheel/tooth wheel. Checking the Flywheel / Tooth Wheel START the engine and let it run at idling speed. Look up the DTC parameter list. Read off the values on flywheel adaption B, C, D and E. The readings should be -97 to +97 . If readings are OK : Check the injectors' current supply. If any of the readings are incorrect : Check the RPM sensor's tip and hole down by the flywheel/connecting flange for signs of damage, scratches and metal shavings. If the RPM sensor and hole are OK : Test with a new flywheel, reset the adaption. Checking the Injectors' Current Supply Check the leads between the injectors' connector 1 and the main relay (2/32) connector 3, as well as ECM A41 and main relay (2/32) connector 1 for signs of an intermittent break. Check also the connectors at the injectors, main relay (2/32) and ECM for signs of loose connection, contact resistance and oxidation. Rectify as necessary. Then continue with: Checking the fuel pump's leads and connectors. Checking the Fuel Pump Leads and Connectors Check the leads between the following components for signs of an intermittent break, intermittent short circuiting to ground and intermittent short circuiting to voltage supply: ECM B27 and fuel pump relay connector 4. Fuel pump relay connector 2 and ground connection 31/51. Battery positive terminal and fuel pump connector 1. Fuel pump relay connector 3 and fuel pump connector 1. Fuel pump connector 2 and ground connection 31/48. Check also the connectors at the following components for signs of loose connection, contact resistance and oxidation: ECM. Fuel pump relay. Ground connection 31/51. Electrical distribution unit. Relay 2/31. Battery positive terminal. Connectors 24/2 and 24/4. Fuel pump connector C/BA and ground connection 31/48. Rectify as necessary. Then continue with: Checking air leakage. Checking the Air Leakage Check if there is any air leakage. If there is no air leakage : Check the engine oil level. If there is air leakage : Rectify as necessary. Then continue with: Checking the engine oil level. Checking the Engine Oil Level Switch Ignition OFF. Check the engine oil level. The oil level should be between the min. and max. markings . If the oil level is OK : Check the fuel and residual pressure. If the oil level is incorrect : Top up to correct oil level. Then continue with: Checking the fuel and residual pressure. Checking the Fuel and Residual Pressure Check the fuel and residual pressure.
-
5-4-2 MISFIRE MORE THAN 1 CYLINDER Preconditions for DTC If the ECM registers more than approx. 6 - 50% misfiring during 1000 engine revolutions (2500 ignition sequences ), the ECM will check if this misfiring comes from one specific cylinder or from different cylinders. If only one cylinder exceeds the limit, DTC 5-4-3 is set first, followed by one of DTCs 4-5-1, 4-5-2, 4-5-3, 4-5-4 or 4-5-5 depending on the relevant cylinder. If several cylinders exceed the limit, DTC 5-4-3 and 5-4-2 are set as well as a DTC for the relevant cylinder. Substitute value Fuel trim with rear Heated Oxygen Sensor (HO2S ) shut off. Fault sources: Defective spark plugs, ignition cables, distributor cap/rotor, ignition coil or flywheel/tooth wheel. Faulty spark plug. Blocked/leaking injector. Uneven compression. Leakage between cooling system and cylinder. Moisture, flashover in ignition system's high-tension section. Intermittent break, intermittent short circuiting to ground, intermittent short circuiting to voltage supply, contact resistance or loose connection in ignition system's low-tension section, in injector circuit or fuel pump circuit. Too much engine oil. Air leakage. Fuel pressure and residual pressure. Fault sources not included in the fault tracing process, but which may still set a DTC: Fuel stoppage. Insufficient fuel level, resulting in fuel starvation. Water in the spark plug recesses. Incorrect fuel or dirty fuel. Repeated cold starts whereby the engine is never given sufficient time to reach normal operating temperature between each start. Puncture in a front tire. Fault symptoms Engine does not start, or is difficult to start. Engine runs unevenly at idling speed, or jerks severely while driving. Poorer performance. Higher emissions.
-
How many more heads do we have in the trailer?
-
One of the purposes of a MLS gasket is to let the different expansion rates of the head and block expand differently. A true MLS gasket offers forgiveness in that it lets the metals expand and contract differently and not let the gasket fret (tear) during these heat cycles. If you coat a MLS gasket it defeats this purpose.
-
A true MLS gasket must be installed dry with no coatings.
-
I had a 1973 Lincoln MK3 for sale in my driveway. I got ticketed for expired tags. When I went to court the judge said "You can have a new Mercedes buried in your back yard, we can go dig it up and ticket you." The MK3 was gone before I went to court, but the judge still ticketed me.
-
CarQuest offers a large line of gasket material. Go with either Victolex, or Victopac material. They offer many thickness. The part numbers are found near the back of the Carquest gasket catalog.
-
Most likely is or he would have near 0 oil pressure. MUST call Jasper before doing anything to your engine. If you touch it before calling them then warranty to void.
-
Happy Birthday Sully!